45V Vane Pumps with Lower Noise
Key words:
Details
Specifications
Subsidiary Series | Displacement Code | Geometry Displacement mL/r | Use anti-wear oil or Phosphate ester fluid | Water glycol fluid | Oil-in-water emulsion | Min speed r/min | Weight Kg | |||
Max. Pressure MPa | Max. Speed r/min | Max pressure MPa | Max. Speed r/min. | Max pressure MPa | Max. Speed r/min | |||||
45V | 42 | 138 | 17.5 | 1800 | 16 | 1500 | 7 | 1200 | 600 | 34 |
45 | 147 | |||||||||
50 | 162 | |||||||||
57 | 183 | |||||||||
60 | 193 | |||||||||
66 | 212 | 16 | 14 | |||||||
75 | 237 | 14 |
Note: ① When the working fluid is phosphate ester fluid, Max. speed see () value, It uses special sealing (FPM), Prefix [F3-] to the specified model when ordering.
②A transient (Peak) pressure 10% over the Max. pressure rating for 0.5s is allower.
Model code
Installation and Use
1. In installation, the tolerance of concentricity between shaft of pump and motor must be less than 0.10mm(TIR) and the maximum permissible angle error is less than 0.2 degrees by using the flexible coupling; The pump shaft shall not bear the
radial and axial load; The carrier must be firm with good rigidity and can fully absorb vibrations.
2. Fix pipes, especially inlet pipes in accordance with the size of port and assemble safety relief valves in the system( the inlet flow rate is between 0.5 and 1.5m/s ). The regulating pressure of the safety valve shall not be greater than the maximum pressure of the pump; Inlet pipes must be strictly sealed with no leakage; Inlet pipes must be strictly sealed with no leakage; The fuel tank shall be equipped with a diaphragm to separate the bubbles and dirt from the oil; The oil return nozzle should be lower the fluid surface, the minimum depth of 50mm, even in a low, too, when the permissible level of to avoid the formation of bubbles.
3 . Set the suction pressure at pump inlet port : Oil hydraulic oil is + 35 ~ -16.7KPa.The hydraulic oil of water - glycol and phosphate ester was +35 ~-10.1KPa.
4 . In case where the pump is installed on the tank or at the position higher than the tank top cover, the height of the suction port of the pump should be less than500mm。
5.Oil should be kept clean, pipes and tanks must be thoroughly cleaned; Precise filters should be assembled with the advised precision of 25μm in the system, the cleanness level of oil should be within NSA12.Fix the sufficient-volume filter (the rated flow rate should be greater than twice the pump flow )at the inlet of the pump 50mm above the bottom of the tank, with the suggested precision of 100μm(150 mesh).
6. It is recommended to use antiwear industrial hydraulic oils or automotive crankcase oils having letter designations SC,SD,SE or SF with viscosity grades of 32 to 68 cSt at 40℃; Preferred viscosity at rated speed and pressures:
Min.13cSt Min.49℃
Max. 54cSt Max. 65℃
7 . Check the inlet, outlet and direction of rotation before starting the pump. Turn the shaft of pump evenly and nimbly by hand after fixing the pump. It is best to fill the pump with oil for the first time. At an initial operation or at an operation after a long rest, the pump may have difficulty in sucking up fluid; In such cases, an air bleed valve should be installed beforehand on the discharge side or discharge air by slightly slackening the connection on the discharge side. At starting, operate the pump intermittently as far as possible with no load.
8. Do not start the pump when the outlet pressure is lower than the inlet pressure. This will cause work noise and blade instability.
9. Cold start condition : When operating SAE10W oil in the 860 to 54cSt range, the speed and pressure should be limited to 50% or less of their respective rated values until the system has warmed up. Extreme caution must be used when starting units when fluid viscosity are greater than 860cSt, Care should be exercised to warm up the entire system, including remote cylinders and motors.
10. At high temperature, viscosities must not be less than 13cSt, Temperatures should not exceed 99℃ because the expectancy of cartridge kite and elastomers will decrease.
Installation Connection Dimensions
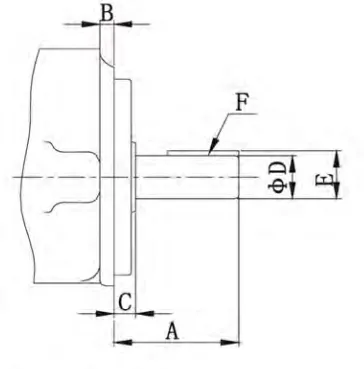
◎ Str. Key shaft
Model | Cold of shaft | A | B | C | D | E | F key Width × Length |
45V | 1 | 62 | 12.7 | 14.2 | 31.75/31.70 | 35.25/35.10 | 7.94 × 28.5 |
86 | 87.4 | 12.7 | 14.2 | 38.075/38.05 | 42.4/42.25 | 9.54 × 50.8 |
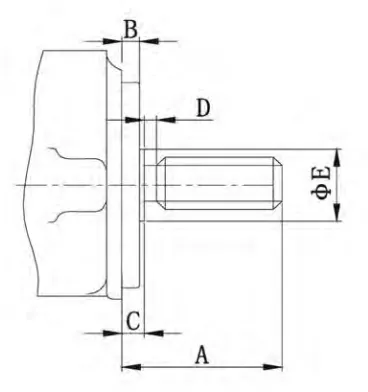
◎ Spline shaft
Model | Cold of shaft | A | B | C | D | E | Spline data | ||||
Number of Teeth | Pitch | Major Diameter | Minor Diameter | Flast root fit | |||||||
45V | 11 | 61.9 | 12.7 | 14.3 | 9.7 | 39.6 | 14 | 12/24 | 31.7/31.67 | 26.99/26.64 | Large diameter fit |
Get Quote
Welcome to leave a message, there may be a discount
Note: Please leave your contact information and our professionals will contact you as soon as possible!